Building an escalation policy - A guide for a first time manager in manufacturing
- Andrew Bissot
- Jul 30, 2024
- 2 min read
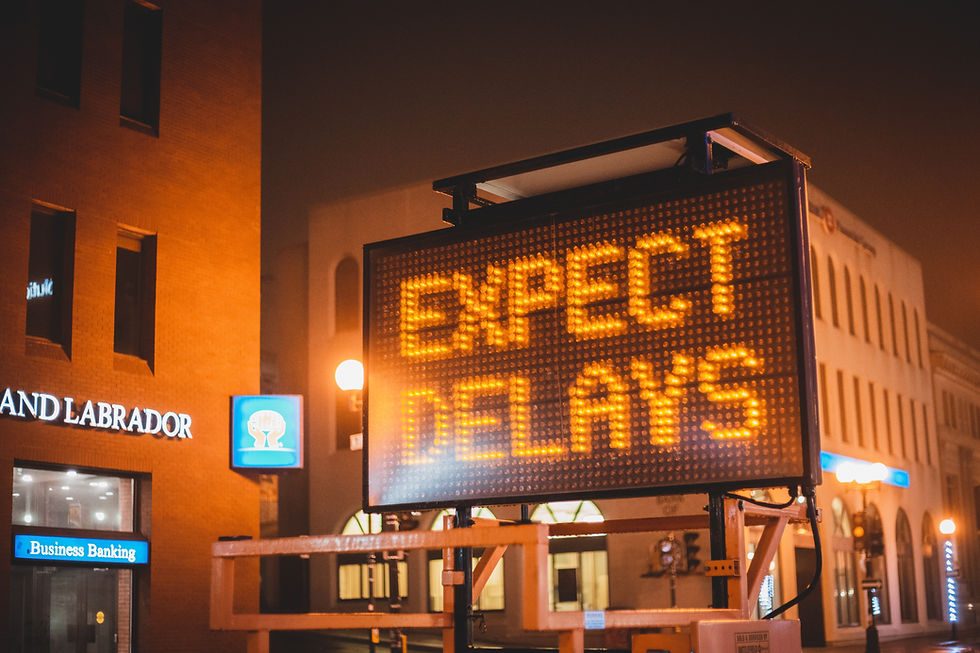
Take a moment and reflect on your first job, where you began managing people responsible for maintaining a manufacturing facility. You were eager to meet the new team members and establish the foundational components of your legacy. If you had a superb mentor, you might have previously actively participated in an escalation policy, which is a rinse-and-repeat for your new responsibilities. This escalation policy would establish the framework where you wanted to get involved in a situation, regardless of the date, day, or time.
Escalation Policy
An escalation policy is the predefined set of situational triggers that an organization would follow before escalating due to their severity, issue, or problem. During an incident, the escalation validates communication is established up the organizational hierarchy and that the appropriate attention is being given to the incident to minimize the severity and impact on operational efficiencies.
An example of a production manager’s escalation policy
You also may be in your first management situation and are looking for examples that you could use to build your escalation policy. To do so, you want first to cover the areas of the business that are indicators of a successful shift while also monitoring delinquency that could impact your reliability. You also want to reference an internal or external standard that emphasizes the why, a description of how to calculate how it is determined to be urgent, and what action needs to be taken.
If you need some help building one, below is an example focused on safety, environmental stewardship, company reputation, current production effectiveness, and vulnerability of asset integrity. Below is an example of an escalation policy to get you started.
Standard/Reference | Escalation Point | Notification Type |
OSHA 1904.7 - OSHA Recordable | An injury involving an employee that will likely result in a recordable incident or lost time. | A phone call, less than 30 minutes from the time of the incident |
A severe incident without injury, that could have resulted in a serious incident or fatality | A phone call, less than 30 minutes from the time of the incident | |
Environmental Permit Exceedance | An incident that will result in a violation of an environmental permit or has a high likelihood that it will | A phone call, less than 30 minutes from the time of the incident |
Company Reputation | An incident involving a team member or assets, that is likely to be known within the community that could drastically create an unfavorable impact on the brand or reputation of the corporation | A phone call, less than 30 minutes from the time of the awareness |
SMRP 2.1.1 Overall Equipment Effectiveness (OEE) | An unplanned delay that has exceeded 24 hours of downtime or a situation will most likely delay that will exceed 24 hours | A phone call at the 24-hour mark or within 1 hour when it is determined that the delay will most likely last more than 24-hours |
SMRP 5.4.11 Preventive Maintenance Work Orders Overdue | A preventive maintenance (PM) work order that has a due date >90 days overdue and within the top 10% of the most critical assets | A meeting scheduled and conducted within 1 week with an AIM (what, why) that describes the PM’s intent, how the preventive maintenance aged, and what are the corrective actions to rectify |
SMRP 5.4.13 Preventive Maintenance Effectiveness | A predictive maintenance (PdM) finding that has a condition that is an imminent failure with the top 10% of the most critical assets | A meeting scheduled and conducted within 1 day with an AIM (what, why) that describes the results of the PdM, how it was found and what are the corrective actions to rectify |
SMRP 5.4.6 Work Order Aging | An open work order >365 days old | A meeting scheduled and conducted within 1 week with an AIM (what, why) that describes the work order’s intent, how it got to >365 days old, and what the corrective actions to rectify |
SMRP 5.4.2 Proactive Work | A work request that is > 30 days since creation has not transitioned into a work order, been returned for more information, or been canceled | A meeting scheduled and conducted within 1 week with an AIM (what, why) that describes the work request’s intent, how it was previously reviewed in gatekeeping meetings, and what are the corrective actions to rectify |
Table 1 - Example of an Escalation Policy
Establishing an escalation policy can assist in removing the vagueness of when leadership should be notified. It maintains a balance of responsibility to allow supervisors to get through problems without being micromanaged while establishing a conduit to gather additional support. Take a moment, and consider how an escalation policy may help you.
Comments